
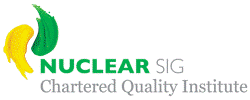
Quality Tools

Performance measurement methods and Quality tools support, develop and aid an organisations continuous improvement process by providing the ability to detect problems, determine their root cause, plan and develop any corrections and validate the solution effectiveness thus leading to continuous improvement and customer satisfaction.
Single tools may be described as methods which has a clear role within an organisation but can be narrowly focused, usually used in isolation which is a common mistake made by organisations.
Organisations often consider tools as separate isolated quick fix instruments and often disheartened when quality tools do not work exactly how anticipated leading to regression productivity and employee disempowerment due to misunderstanding or incorrect application.
There is a saying that helps summarise the utilisation of quality tools in isolation by an organisation who have misunderstood their intended use or ability, that if you only have a hammer in your toolbox it is surprising how many problems look like nails (Dale, Bamford & Wiele - Managing Quality- 2016).
Most organizations use basic quality tools for various purposes and applications related to controlling and assuring quality.Although a good number of quality tools are available there are a number of tools that are quite generic and can be applied to any sector.
These tools can be utilized by Quality professionals to provide related information and understanding about problems in the organization and assisting to derive solutions.
Some Quality tools are described below:
Plan, do, check Act
PDCA, sometimes called PDSA, the "Deming Wheel," or "Deming Cycle," was developed by renowned management consultant Dr William Edwards Deming in the 1950s. Deming himself called it the "Shewhart Cycle," as his model was based on an idea from his mentor, Walter Shewhart.
The four phases are:
-
Plan: identify and analyse the problem or opportunity, develop hypotheses about what the issues may be, and decide which one to test.
-
Do: test the potential solution, ideally on a small scale, and measure the results.
-
Check/Study: study the result, measure effectiveness, and decide whether the hypothesis is supported or not.
-
Act: if the solution was successful, implement it.
5-Whys
Sakichi Toyoda, one of the fathers of the Japanese industrial revolution, developed the technique in the 1930s. He was an industrialist, inventor and founder of Toyota Industries. His method became popular in the 1970s, and Toyota still uses it to solve problems today.
The 5 Whys technique is true to this tradition, and it is most effective when the answers come from people who have hands-on experience of the process being examined. It is remarkably simple: when a problem occurs, you drill down to its root cause by asking "why?" five times. Then, when a counter-measure becomes apparent, you follow it through to prevent the issue from recurring.
This simple technique, however, can often direct you quickly to the root(s) of a problem. So, whenever a system or process isn't working properly, give it a try before you embark on a more in-depth approach – and certainly before you attempt to develop a solution.
FMEA (Design & Process)
By looking at all the things that could possibly go wrong at design stage, you can cheaply solve problems that would otherwise take vast effort and expense to correct, if left until the solution has been deployed in the field. Failure Modes and Effects Analysis (FMEA) helps you do this.
More than this, FMEA provides a useful approach for reviewing existing processes or systems, so that problems with these can be identified and eliminated.
Examples When to use FMEA:
-
When a process, product or service is being designed or redesigned, after quality function deployment (QFD).
-
When an existing process, product or service is being applied in a new way.
-
Before developing control plans for a new or modified process.
-
When improvement goals are planned for an existing process, product or service.
-
When analysing failures of an existing process, product or service.
-
Periodically throughout the life of the process, product or service
Ishikawa diagram (fish bone)
Also Called: Cause-and-Effect Diagram or Fish bone, this cause analysis tool is considered one of the seven basic quality tools.
The fishbone diagram identifies many possible causes for an effect or problem. It can be used to structure a brainstorming session. It immediately sorts ideas into useful categories.
When to utilise this quality tool:
-
When identifying possible causes for a problem.
-
When a team’s thinking tends to fall into ruts.